The ball mill of grinding equipment
The ball mill is the most common grinding equipment in the grinding plant. The ball mill is the key equipment for the material to be crushed and then crushed. It is widely used in cement, silicate products, new building materials, refractory materials, fertilizers, ferrous and non-ferrous metal beneficiation and glass ceramics and other production industries, dry or wet grinding of various ores and other grindable materials. Ball mills are suitable for grinding various ores and other materials. They are widely used in mineral processing, building materials and chemical industries. They can be divided into dry and wet grinding methods. According to the different discharge methods, it can be divided into grid type ball mill and overflow type ball mill.
The so-called "stubborn stones" (also known as critical particles) generally refer to the fact that when the ball mill grinds ore, due to the small number of medium and coarse particles in the grinding ore, it is easy to form a kind of grinding medium that is too light in the ball mill, and is used as a ball mill. The 30-50mm size nuggets that the grinding products cannot be discharged through the grid holes. These ore blocks (stubborn stones) gradually accumulate in the mill, occupying the volume of the mill, resulting in a decrease in the output of the autogenous mill, an increase in the unit power consumption and the phenomenon of over-grinding.
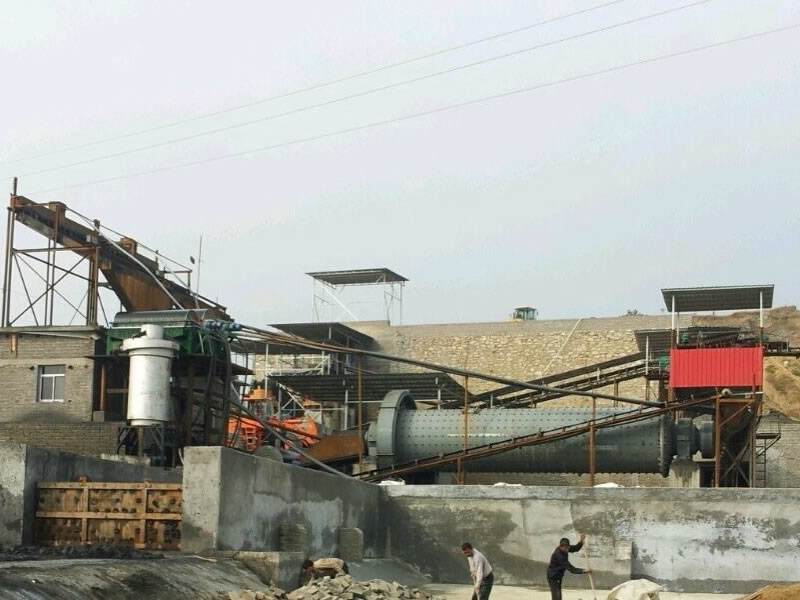
To eliminate or prevent the accumulation of stubborn stones in the ball mill, the following methods can be taken:
1. The self-grinding-ball-milling-crushing process is adopted, that is, the self-grinding open-circuit grinding process is adopted, and the material on the screen of the discharge cylinder is drawn out, and after being finely crushed and crushed by a ball mill, it is combined with the product under the screen for processing. This is the so-called A-B-C grinding process.
2. Use ball mill semi-autogenous grinding, that is, add large steel balls (ball diameter 100-150mm) with a filling rate of 5% to 8% into the autogenous mill to supplement the lack of energy and grinding of large pieces of medium. critical particle".
NEXT: How to configure the cobblestone sand production line